Robert Bollinger is the founder and CEO of Bollinger Motors – the New York-based startup that is developing a tough, fully electric off-roader. Last month he took time out to tell GreenMotor about the progress he and his team of engineers have made since the boxy but brilliant B1 design was first revealed last summer.
GreenMotor: It’s a year since we first saw the B1. What progress have you made in getting your electric SUV from prototype to production readiness? And who’s going to build it?
Robert Bollinger: Originally we were going to find a third party contract manufacturer to make the B1 for us, but we haven’t found anyone in the US that’s really set up for that. So we’ve decided to take on the assembly ourselves, relying on partnerships with our suppliers to make major components.
I’m very excited about that decision, because we can take control of things like quality and timing and everything like that.

Q: Does that mean your first customers will get hand-built vehicles?
Yes, exactly. With that, our initial start-out volumes have come down. We aim to do things really, really well, and our number one goal is to get the truck made. It also means the price of the first vehicles will be higher than we anticipated but once we get out there, and start growing, we can grow towards better price points.
Q: What have you learned from taking your prototype B1 out for testing in the US?
It’s been through a lot of testing now – real world testing on my farm, and then we took it out west [to Moab in Utah, and to the San Juan Mountains near Ouray, Colorado]. We also put it on the test track, bringing it up to road speeds and checking the batteries, seeing that they’re discharging correctly, that the motors are using the power at the level we expected.
Then we took the vehicle apart again, looked at all the gearboxes to see if there was any build up of anything, if anything got in or leaked out. So it’s all that kind of very pragmatic, hands-on kind of testing that we’ve done with our prototype.
More recently we’ve put tons of sensors all over it and put it through a durability test track. We take all the data from that and then we can simulate hundreds of thousands of miles of use, and then engineer to those standards. We want the truck to last forever, but what does that mean in the real world? How many hundreds of thousands of miles do we want to engineer it to?
Next year, after that optimisation work, we’ll make new prototypes of the real production version and we’ll take them back to that durability test track and run for thousands of miles, take that data and extrapolate that to make sure we’ve engineered it to the right level.

Q: Have you designed your own testing schedule or are you following the kind of processes used for conventional vehicles?
We are working with experts who have a lot of past experience in testing at the big three [Ford, General Motors and Chrysler]. There are all these different companies out there that can do an incredible amount of testing for you. They can do everything.
Our engineering partner, Optimal, also has a lot of experience in benchmarking other vehicles and we’ve set up our targets together.

Q: As a tough, off-road EV, the B1 is unique – there’s nothing to compare it to. What are you benchmarking it against?
We’re taking everything that’s out there, acknowledging it, and then choosing where we want to be. It’s kind of a mishmash of things. So on durability we want to beat this truck, for electric safety we want to be as good as that vehicle. We have three main vehicles that we’re benchmarking against, for completely different reasons.
We also look at what trends are happening: where body stiffness values are going on vehicles and what’s going to be expected in a couple of years, so that when we come out in another year and a half we’re still ahead of the game. And we’re constantly seeing where we stand in the group of all electric vehicles.

Q: Presumably it was that kind of forecasting that triggered your switch to a 120kWh battery pack, instead of the 60kWh and 100kWh options you initially planned to offer?
With the B1 being electric and low volume, it’s going to be at a certain price point. There’s just no way around it, it’s not going to be cheap. And since the truck is so capable, we thought we can’t cripple it with a small battery pack. Even though the battery is the single most costly portion of the vehicle, we’re not going to save that much. So really we thought: let’s just go full-on, flat out; this is the vehicle you’re going to want.
It’s twice as much work to develop two battery packs, so the fewer options we have the better. It’s going to be a huge pack but, you know, the truck is just kind of over-the-top in all other regards.
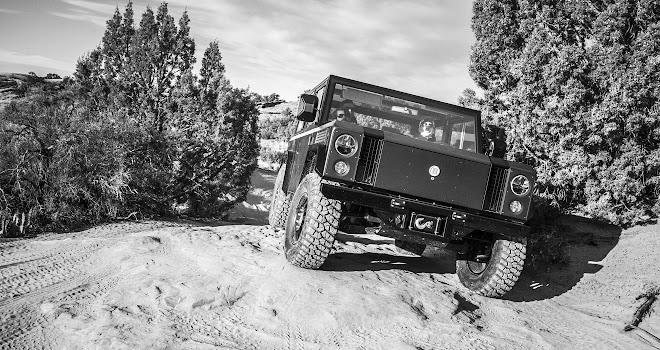
Q: Does the bigger pack affect the size of the B1 inside or out?
The slightly longer wheelbase of the 4-door helps give us a little more room for the bigger battery. It’s all fitting in there nicely now within the same outer architecture. It still has exactly 15.5-inch ground clearance, still has 10-inch wheel travel. The only difference externally is that it’s 12 inches longer in the wheelbase.
We’ve also changed battery cell vendors, and we’ll have an initial 4-door prototype to take out and get a feel for later this summer, into the fall.

Q: Given the advantages of standardisation, will the 4-door model supplant the 2-door we first saw and become the only B1 customers will be able to buy?
The 4-door will be the first to come out, but we do want to have the 2-door and other vehicles after that.
I was answering all the emails and looking at the comments online, and so many people were enquiring about the 4-door. The Jeep Wrangler Unlimited is a good comparison. When that came out, people were like: “Don’t mess with a classic”, but now 90% of Wranglers are bought with four doors. If we try to engineer both the 2-door and the 4-door at the same time it will just delay us, but the idea is to have more versions down the road.
